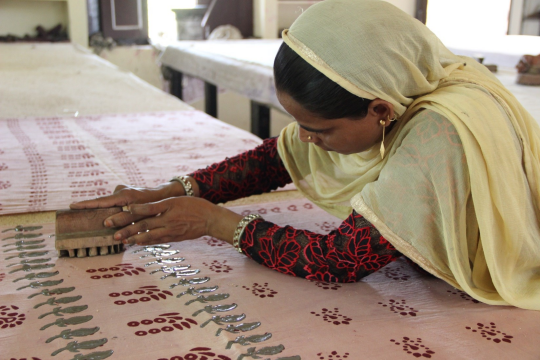
Ever Wondered How Dabu Prints Are Made?
Share
Dabu Printing: An Ancient Craft Reimagined
Dabu printing, an age-old resist printing technique, weaves together tradition and artistry to create mesmerizing patterns on fabric. Rooted in Indian heritage, this labor-intensive craft involves intricate processes that bring a unique charm to every piece. Here's a breakdown of how this beautiful art form comes to life:
1. Preparing the Fabric
- Pre-Wash and Soak: The fabric is soaked in water mixed with turcoil oil for 24 hours. This step removes starch, dust, and other impurities.
- Beating: The fabric is then beaten to ensure it is clean and ready for dyeing.
- Harda Dye Bath: The fabric is immersed in a Harda (merubelum powder) solution, giving it a yellow tint while ensuring natural dyes adhere and become colorfast.
2. The Creation of Dyes
- Syahi (Black Dye): A mixture of horse shoe iron, water, and jaggery is fermented in an earthen pot. This process takes 15-20 days in summer but stretches to 6 weeks in winter. Tamarind seed powder is added and boiled to complete the Syahi preparation.
- Begar (Red Dye): A vibrant red is created by combining alum (fitkari), madder (lal mitti), and babool gond juice.
3. Block Printing Process
- Setting the Fabric: The dyed fabric is spread on long padded tables to begin the printing.
-
Three Types of Blocks:
- Gadh Block: Used for the background.
- Rehk Block: Creates fine outlines.
- Datta Block: Adds intricate inside patterns, often involving multiple blocks for different colors.
- Repetition and Precision: Each block is carefully applied multiple times to achieve the desired design, ensuring the motifs align perfectly.
4. Drying and Washing
- Natural Drying: After printing, the fabric is left to air dry, allowing the colors to settle.
- Multiple Washes: The fabric is washed 3-4 times in fresh water to remove excess dye and impurities.
5. Boiling for Final Color
- Copper Pot (Bhatti): The printed fabric is boiled for about 5 hours in a mix of natural ingredients like alizarin (aal ki lakdi) and sakura flower (dawari ka phool).
- Harda Treatment: A final dip in the Harda solution removes any remaining alum, ensuring the colors remain vibrant and long-lasting.
6. Finishing Touches
- Roll Pressing: The fabric is roll-pressed to give it a polished and crisp finish.
- Ready to Adorn: The block-printed masterpiece is now ready to charm with its unique blend of traditional craftsmanship and contemporary appeal.